Space and Time. Are You Considering the 4th Dimension in Product Development Data?
An introduction to how smart data utilizes information and actionable context to support business-critical decisions.
It may sound fanciful to equate the medical device design and manufacturing industry with taking a journey through space and time. However, given that time and numerous iterations need to be factored into design work, planning, and processes, plus the need to manage, approve and track all decisions and changes made when, by whom, and for what reason, it is precisely that.
Failure at Critical Preproduction Stages Comes at a Potentially Significant Cost
Mistakes in the early stages of product development can bloom into bigger issues later on. At best, a wrong step in preproduction, along with insufficient paperwork, can delay a program. At worst, it can force going back to the design concept, where a manufacturer may have to chalk their efforts up as a lost project.
For start-ups, a lack of transparency with respect to design history could prove a fatal game changer, not only for submissions, but also when investors need confidence in the business as well as an understanding of likely returns. Either way, failure at R&D and critical preproduction stages comes at a potentially significant and damaging cost.
One way to allay these issues is to have a clear audit trail so that interrelationships (and potential issues between them) are easily visible. In addition, health authorities such as FDA in the US or Notified Bodies in Europe require an audit trail—the kind that pulls together predictive thinking and clear processes, and goes beyond simple traces. This cannot be emphasized too much. But facilitating a clear audit trail can be complicated based on the tools used today.
Interestingly, many industries still have some proponents of spreadsheet (Excel) or even document (Word) tables. While an increasing number of companies understand the limitations these tools impose on the aforementioned processes, in more straightforward production environments they can serve a purpose.
As we pointed out previously in another post, Three Key Questions for Assessing Medical Device Risk Management Tools, there's nothing wrong with the use of spreadsheets and simple tables for projects up to a certain complexity. But even low-complexity projects become hard to manage once risk assessments and test management are fully integrated, meaning that many-to-many relationships between requirements, risks, and test data items need to be tracked and maintained—and not only once, but also over time.
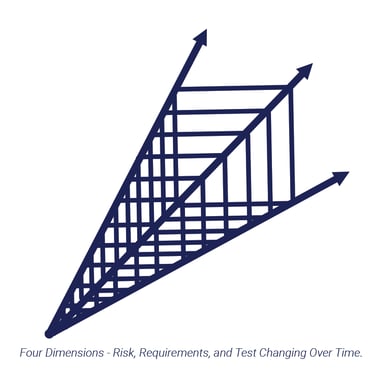
Increasingly, Cognition has become recognized as the software tool of choice for medical device and pharmaceutical manufacturers, and that’s because of an exhaustive and evolving focus on providing an environment that manages the whole spectrum of data items (complete documents as well as individual items such as requirements, hazards, hazardous situations, harms, or tests and test steps, to name but a few), while supporting those with a process that directs and governs these items through time. Managing this evolution of data is what we call the fourth dimension.
So, how does the fourth dimension factor into medical device design and manufacturing? Let’s look at all the dimensions.
Engineers Squeeze Information Into One Dimension Due To Limitation Of Tools
Simple spreadsheet and table models (such as Word or Excel) can cope with linear hierarchies—top to bottom data—but they do not allow for easy management of relationships between separate document tables. For example, reusing data between two tables necessitates copying and pasting the entry, which then needs to be managed manually in case of changes, as the tables have no linked relationships. This approach works with small documents where needs are modest and/or limited. An example would be a requirements hierarchy with requirements and sub-requirements; we call this the first dimension.
As each individual requirement would need to be verified/validated, adding test data would produce the second dimension.
Adding risk information expands the data set into the third dimension.
Requirements, as well as test information, might correlate to risk information, such as requirements being affected by failures that can cause harms, or tests being part of a mitigation strategy to mitigate risks.
The data, however, is not static, but rather evolves over time with many changes. This evolution over time is what we call the fourth dimension.
A robust data model cannot be based on simple tables, in which contextual information for a data cell is largely limited to being next to neighboring data cells. Truly contextual information, however, requires the management and display of many more data “linkages,” all managed in a database.
It must be possible to analyze, manipulate, and use this information, and in order to become meaningful, it needs to correlate to other information and data points. In many cases, these become complex as data sets need to work with other corresponding and independent data sets. Already, we are getting a picture where spreadsheets or word processor tables might struggle to get to grips with even basic data sets, let alone interdependent data.
If we visualize the requirements/test/risk space as a cube, this structure changes over time, expands or shrinks, adds or takes away connections. The data is dynamic and needs to be captured, connected, and interrelated. The questions of who changed what, where, when, and why need to be answered.
Often, however, design engineers will try to squeeze information into one dimension, due to the limitations of the tools made available to them.
Because We Understand Customer Challenges, Cognition Takes That Headache Away
In medical device design, there are a number of questions about relevant data that need to be answered:
- What are the different tools we can use to get a more accurate picture of the data?
- How do we track, monitor, and manage how, why, and by whom the data is changing?
- What is the relationship with other pieces of data?
Once these questions can be answered and the data is efficiently managed, you are in a better position to be both more proactive and to be more effective with reactive tasks.
At the same time, a fuller/truer picture of the data emerges.
This structured data may be used in multiple locations, exist over time, be reusable, be connected in various hierarchies and relationships, and enable action at a distance. Due to the database nature of these data items, updates to an item are pulled or pushed through to all locations that use the same item.
“Four-dimensional data” might sound complex to manage, but it is a way of making sense of how data can be managed, analyzed, and made to work for you; avoid the problems posed by standard tools such as spreadsheets and tables; and help produce the required deliverables.
Because we are focused and understand customer challenges for medical device designers and manufacturers, our solutions take that headache away. Our software automatically maps the data relationships and how each is relevant and connected.
See why four dimensions of data is the future of medical device product development data management. Request a demo today!