Cultivating Risk Focused Design Instincts
Medical Device | Product Development | Risk Management | Design | Process | Documentation
How a risk-based design approach provides safer and ultimately better quality products to market.
Product designs are stronger when risk is inherently considered. Not everyone has the experience and instincts to naturally consider the critical factors required in a comprehensive approach. A solid process ensures risk is addressed consistently throughout product development by all of the stakeholders. It is not enough to intuitively consider risk when designing a product; decisions need to be articulated and documented - this documentation is used to support the design choices throughout the product's life.
Taking a Risk-Based Approach
Rather than treating risk as a check-the-box exercise at the end of development, a risk-based approach focuses the team on design for quality and safety. This helps identify the “why” in product design and is tracked in the design history file (DHF) or design and development file (DDF) in order to show product iteration.
A risk-based design approach challenges assumptions, which leads to safer and better products. Some key elements of a risk-based design approach include:
- Analyzing user or patient risks
i.e., ease of use, safety, ergonomics, etc. - Identifying, documenting, and quantifying points of risk
i.e., failures, complaints, hazards, etc. - Evaluating business risks
i.e., cost, time, suppliers, regulations, etc. - Creating mitigations for risks and harms
i.e., tests, design, poka-yoke, etc.
Good Design Instincts Are Not Enough
Good risk assessment starts with good designers. Good designers who have experience automatically assess risk throughout the design process. They evaluate risk from raw materials through product usage and eventual decommissioning. They consider how a design decision may impact multiple factors (manufacturability, functionality, safety, etc.) as they conceptualize the product to meet the intended use and unmet needs of the market. Since many of the design choices are done in the earliest concept stages, the rationales associated may not be formally documented. These considerations, however, are critical to the future sustainability of the product. Documentation helps guide future design decisions and changes as the product goes through its lifecycle. Good designers leverage their experience to make logical and thoughtful designs and they can articulate their logic. The challenge is to formalize these good design instincts into a process that can be followed by the entire design team.
Developing a Strong Process
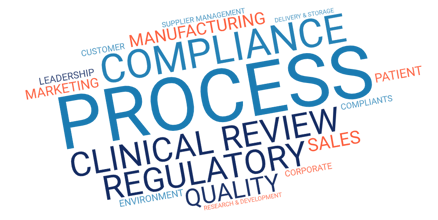
We can’t hire an entire team of experienced designers with risk assessment in their bones. Therefore, we need to develop the framework of a good designer into a strong process that results in good design practices. This process must be all-encompassing, taking a holistic view of design from multiple perspectives including but not limited to:
Clinical Review: Are there similar products that can be assessed for baselines and to improve known issues? What can be gathered to better understand usage and knowledge of the procedure and indications?
Complaints: What can we learn from what has gone wrong? How can we leverage our understanding of root causes to mitigate similar issues?
Compliance: What do the standards and regulations require?
Corporate: What is the ROI? How can business risks be reduced? How do we reduce time to market and maximize margin?
Customer: What is the voice of the customer? What is the intended use? What are the safety concerns?
Delivery and Storage: What are the limitations and considerations for package size, protection of the product, maintenance of sterility, material stability, etc.?
Environment: What are the methods of disposal, recycling, or reuse? What is the material impact on the environment?
Leadership: How is employee safety ensured? What are the risks to the market/users/patients?
Manufacturing: How will this assemble on the manufacturing floor? What are the risks within the process? Is it repeatable and reproducible to make? What is the efficiency of the process?
Marketing: How will the customers interact with the product? How do we make it stand out? What is unique and new? What is the story around it?
Quality: What does the internal process define? Where have internal noncompliance observations been identified in the past? What risks are similar to other products? What has been seen by their experience at other companies?
Patient: What are the side effects? What are the risks of the procedure? What is the benefit of the product versus the risks?
Regulatory: How do the process and design account for mandates from governing bodies?
Research & Development: How does this design meet unmet needs in a way that is safe and effective? What can be leveraged from other designs? What is the risk to the patient?
Sales: How is it differentiated from other products? What problem does it solve? What is the price point and margin?
Supplier Management/Quality: What are the risks from the supply chain? Are there concerns from the suppliers?
The earlier in the process risks are addressed, the faster the design can iterate and the cost of change minimized. When a strong, sustainable process is in place, a company will see reduced costs through consistency, increased productivity through reduced troubleshooting or variability, and can be confident that the products they design are high quality.
Putting a Risk-Based Approach into Action
Talking about taking a risk-based approach to design is easy; however, putting it into action can be challenging. Below we have provided a simplistic example of how a designer may approach the design of an instrument while remaining risk-focused throughout the process.
Consider an instrument that is used to insert an anchor/screw into bone. Although it resembles a screwdriver, you cannot simply grab one from your toolbox.
This instrument is part of a system as a classified medical device and must adhere to 21 CFR 820, ISO 13485, and ISO 14971, among other regulations and standards.
Some key considerations in the design process of this instrument:
- Biocompatibility: Which materials will produce the best product while optimizing usability and safety for the patient?
- Failure Method: Is it better for the instrument itself to break or for the implant to fracture? Which is safer for the patient?
- Infection: What happens if a disposable device is reused? How can the design prevent reuse? What would make the instrument reusable?
- Costs: What is the minimum cost of materials without losing needed functionality?
- Production: How easy is it to manufacture, assemble, and package?
- Functionality: What are the ergonomics? Is the instrument strong enough? Does it interact with the product?
While a good designer may automatically consider these factors when a solid process is in place, all designers will consider:
- The biocompatibility of all materials
- The optimal failure method for the instrument to keep the patient and doctor safe
- The molding process to optimize the design for less material, faster cycle time, cost, etc. as well as many other considerations.
With a strong, sustainable process, even the simplest medical products will have documentation of key considerations made during the design process.
Choose Compass for a Risk-Based Design Approach
A process is only as good as it is followed. If you develop a risk-based design approach but do not have parameters to make sure it is followed, your process is worthless. Enter Compass, a preconfigured SaaS solution that has been foundationally designed to leverage regulations such as 21 CFR 820.30 as well as standards ISO 13485, IEC 62366, and ISO 14971. The built-in workflows ensure cross-functional collaboration via defined roles, review processes, and approvals. Comprehensive linkages between requirements, risk, and test enable the designer to easily consider risk early in the design process and provide an audit trail throughout the product’s lifecycle. Compass’s intrinsic process walks through the design development steps connecting risk along the way with mitigations tied to inputs and outputs. See our blog post on why leveraging a regulation/standard-based process is the best practice for quality design.
Interested in learning how Compass can help ensure your team takes a risk-based design approach?