Stay Ahead of the Curve: 10 Ways to Achieve Medical Device Compliance
Medical Device | Risk Management | Compass | Design | compliance | Regulations
Save time and money by addressing regulations early and often
Medical device engineers are tasked with developing innovative and safe products while meeting a multitude of regulations in an ever-changing landscape. Meeting these regulations can be challenging and expensive, especially for startups and smaller companies. Here are 10 ways to help medical device engineers meet regulations without wasting their design budget or timeline:
1. Understand the Regulatory Landscape 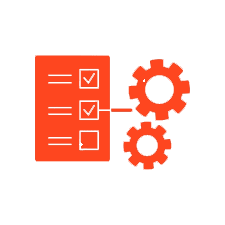
It is important for medical device engineers to have a thorough understanding of the latest regulations specific to their product. They should be familiar with the regulatory bodies that oversee their device and the specific regulations that apply to it. This will help them design their device with compliance in mind from the outset, reducing the risk of costly changes later on. Training the team to understand the regulations, standards, and reasons why these are in place fosters a compliance mindset. Addressing required specifications or tests early on allows for timely course correction and reduces the risk of having to overhaul the design at a later, more expensive stage.
2. Design with Compliance in Mind
Designing with compliance in mind can help prevent costly design changes later in the development process. Engineers should consider country-specific regulations throughout the design process. For example, leveraging design controls as defined in 21 CFR 820 Part 30 supports not only compliance with the regulation, but provides evidence that the device is safe, works as expected, and meets the market needs. Using already established standards, such as ISO 13485: Quality management systems and ISO 14971: Application of risk management to medical devices, can help ensure compliance via consensus standards with regulations. Cognition’s software has been designed specifically for the medical device industry, incorporating feedback from leading companies and following best practices of consensus standards.
3. Adopt a Risk-Based Approach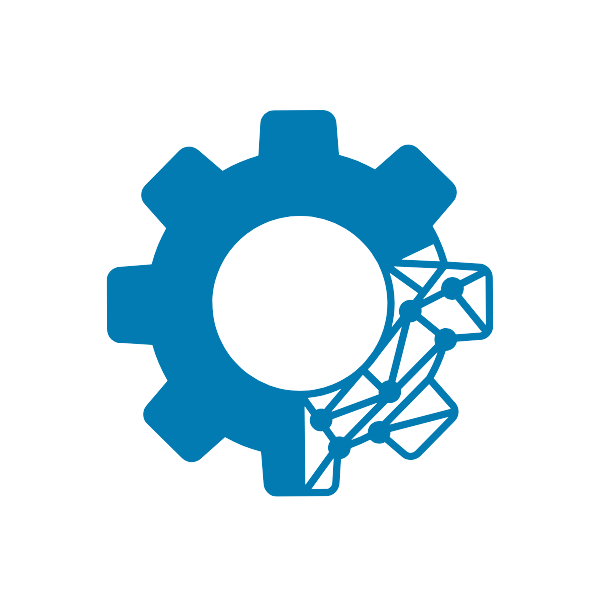
Prioritize development efforts based on product risk. Focus first on the most critical areas that have the highest potential impact on safety and effectiveness. By identifying potential risks early on, engineers can design their device to minimize those risks, reducing the likelihood of the need for costly post-market design changes. This approach allows for targeted resource allocation while still meeting regulations for the crucial elements of the device. A risk-first approach also helps identify areas to test or additional requirements that may be necessary. Cognition’s risk offerings have been built to comply with ISO 14971 and to enable tailoring to a customer's specific process. Read more on the importance of a risk-based approach here.
4. Utilize Predicate Devices/OTS Components
By using existing device data or off-the-shelf (OTS) components, engineers save money while ensuring compliance with regulations. Engineers can leverage, mitigate, or decrease the need for expensive and extensive testing by using components that have testing on file, or are used in a cleared medical device. Keep in mind that utilizing what is existing doesn’t necessarily mean physical components only; other engineers experienced with moving through the design, development, submission, and production processes can help!
5. Test Early and Often
Testing is a critical part of the design process for medical devices. By testing early and often, engineers can identify issues promptly and make necessary changes before they become a more expensive problem to address, consuming both time and money. Testing may be used to verify if a requirement was met, mitigate a risk and verify its effectiveness, identify areas of concern, or demonstrate that standards are being met. All requirements are verified or validated, primarily via testing. Compass and Cockpit Enterprise softwares’ core strength is creating connections and traces between elements, ensuring that nothing is missed. The ability to create tests within the software simplifies the need for a separate system and can instantly track test coverage.
6. Conduct Early and Frequent Design Reviews 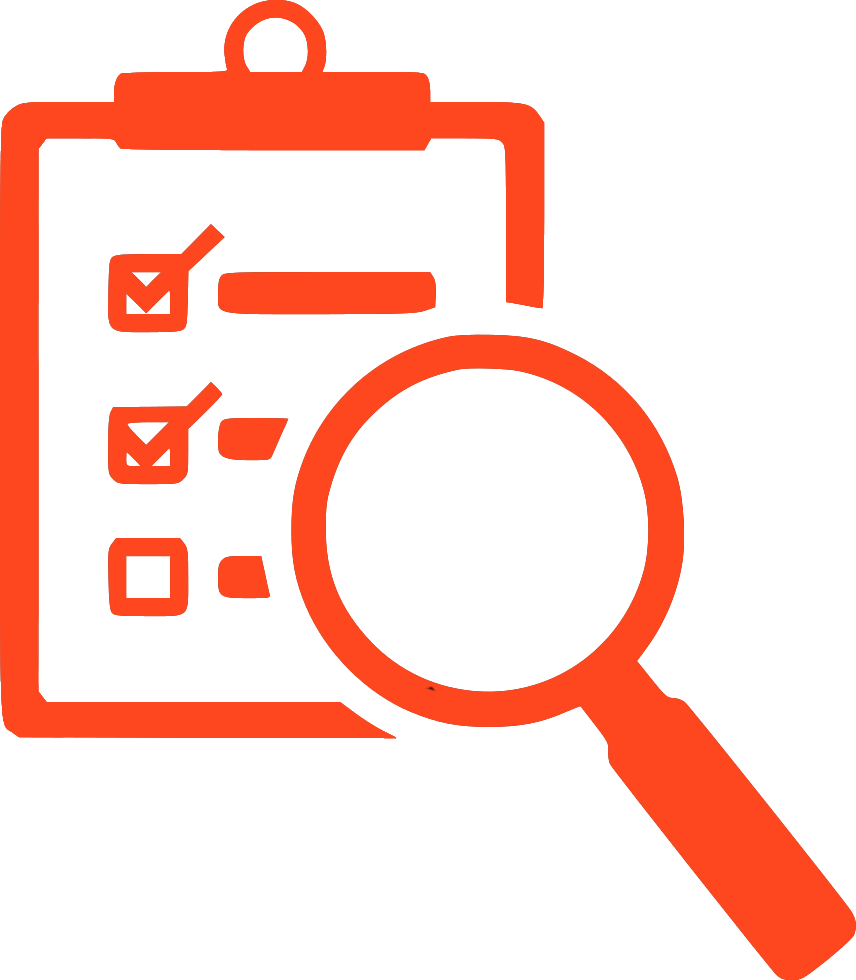
Regular design reviews involving cross-functional teams, including regulatory experts, are essential. These reviews are not just a formality but serve as a critical checkpoint to catch potential compliance issues before they turn into costly problems. Regular reviews at various milestones provide an opportunity to assess progress, evaluate compliance status, and identify any emerging concerns. With collaborative design reviews, a culture of shared responsibility is fostered via open communication, knowledge exchange, and early identification of potential roadblocks. The expertise of regulatory professionals combined with the insights of other team members ensures that compliance considerations are woven into the design process from the very beginning.
7. Follow a Quality Management System Process
A well-designed QMS reduces errors, optimizes resource allocation, and confirms that processes are consistent and in line with regulations. By working within a Quality Management System (QMS) throughout the design process, engineers can ensure that their device is designed to meet applicable regulations and standards, which will save both time and money by reducing the need for expensive changes late in the project and demonstrate consistency across projects and products. Use of Compass or Cockpit Enterprise can help companies enforce a process with consistent documentation, workflow, and data.
8. Conduct Continuous Internal Auditing
Continuous internal auditing is a key pillar in the realm of compliance for medical device companies. It involves establishing a robust system that allows for continuous improvement via regular and thorough assessments of processes, documentation, and practices. The beauty of continuous assessment lies in its proactive nature. Rather than waiting for external audits or regulatory inspections, employees take ownership of compliance and identify areas of improvement in real-time. All employees can identify bottlenecks, inefficiencies, or gaps in compliance. They can then take corrective measures, whether it's refining processes, updating documentation, or implementing new practices.
9. Engage with Regulatory Bodies Sooner, Rather than Later
Don't wait until the last minute to engage with regulatory bodies. Establishing open lines of communication early on helps clarify requirements, obtain guidance, and prevent costly delays or misunderstandings down the road. Early engagement with regulatory agencies can help the team understand the regulations and get guidance on how to comply with them for their specific device. The FDA has a pre-submission process where manufacturers can ask for feedback on their device's design and regulatory pathway.
10. Let Technology Do the Work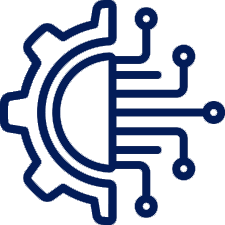
Harness the power of 21st-century technology to streamline compliance efforts. Software tools, automation, and digital documentation systems are readily available and can improve efficiency, accuracy, and traceability, ultimately reducing the time and expenses associated with development and compliance. However, these tools often are viewed as too expensive upfront and time-consuming to research and implement. The long-term payoff of implementing technology pays for itself. For help in assessing tools, check out our guide here.
Staying Ahead of the Curve
When companies take the above 10 methods into consideration, they have a head start on their path to compliance while developing medical devices. By embracing the changing regulatory landscape and creating a foundation of design with compliance in mind, they can be confident they are setting themselves up for success without wasting their design budget or timeline.
Here at Cognition, we have embodied these approaches into our Compass solution, our pre-configured design controls SaaS platform built specifically for medical device companies. Compass helps companies meet regulations faster with real-time traceability, guided design controls, and “change once, update everywhere” functionality—turning manual and disconnected data into structured submissions that enable getting to market faster.
See How Technology Can Work for You!
Request a Demo Today.